News
How To Choose Kaolin Powder Mills?
Date:2021-09-04 09:06:41
What is Kaolin?
Kaolin is also known as "kaolinite" and "china clay". A clay mineral.
Kaolin is a non-metallic mineral, a kind of clay and clay rock dominated by kaolinite clay minerals. Because it is white and delicate, it is also called white cloud soil.
Kaolin is formed by aluminosilicate minerals such as feldspar and pyroxene during weathering. It is earthy or massive, with low hardness, plasticity, adhesiveness and volume expansion when wet, especially microcrystalline kaolinite (also known as "montmorillonite", "jiaolinite") has greater expansion (can be Up to several times to ten times). The main components of microcrystalline kaolinite and belayite are called "bentonite".

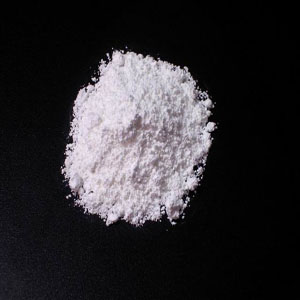

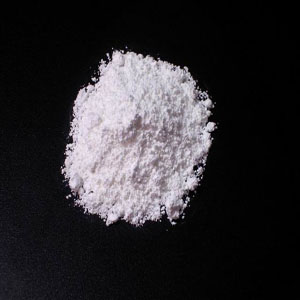
The Characteristics of Kaolin
Kaolin has high whiteness and brightness, soft quality, strong water absorption, easy to disperse and suspend in water, good plasticity and high adhesion, resistance to acid and alkali, excellent electrical insulation, strong ion adsorption and Weak cation exchange, good sinterability and high refractoriness.
The pure kaolin is white, fine, soft and soft, and has good plasticity and fire resistance and other physical and chemical properties. Its mineral composition is mainly composed of kaolinite, halloysite, hydromica, illite, montmorillonite, quartz, feldspar and other minerals.
Applications of Kaokin
Kaolin has a wide range of uses. It is mainly used in papermaking, ceramics and refractory materials, followed by coatings, rubber fillers, enamel glazes and white cement raw materials, and a small amount is used in plastics, paints, pigments, grinding wheels, pencils, daily cosmetics, soaps, etc. Pesticides, medicines, textiles, petroleum, chemicals, building materials, national defense and other industrial sectors.
Ceramic Industry
The ceramic industry is the earliest application of kaolin, and the consumption is relatively large. The general dosage is 20%-30% of the formula. The role of kaolin in ceramics is to introduce Al2O3, which is conducive to the formation of mullite, and improves its chemical stability and sintering strength. During firing, kaolin decomposes to form mullite, which forms the main frame of green body strength, which can prevent the product from degrading. Deformation can broaden the firing temperature and also make the green body have a certain degree of whiteness. At the same time, kaolin has a certain degree of plasticity, cohesiveness, suspension and binding ability, which endows porcelain clay and enamel with good formability, so that the ceramic clay body is beneficial to car blanks and grouting, and is easy to form. If used in wires, it can increase insulation and reduce its dielectric loss.
Ceramics not only have strict requirements on the plasticity, bonding, drying shrinkage, drying strength, sintering shrinkage, sintering properties, refractoriness and whiteness after firing of kaolin, but also involve chemical properties, especially iron, titanium, copper, chromium, The presence of manganese and other color-causing elements reduces the whiteness after burning and causes spots.
The particle size of kaolin is generally as fine as possible, so that the porcelain clay has good plasticity and drying strength. However, for casting processes that require rapid casting, faster grouting and dehydration, the particle size of the ingredients needs to be increased. In addition, the difference in the degree of crystallization of kaolinite in kaolin will also significantly affect the process performance of the porcelain blank. If the degree of crystallization is good, the plasticity and bonding ability will be low, the drying shrinkage will be small, the sintering temperature will be high, and the impurity content will also be reduced; Its plasticity is high, the drying shrinkage is large, the sintering temperature is low, and the corresponding impurity content is also high
In addition to being used as ceramic raw materials, papermaking raw materials, rubber and plastic fillers, refractory materials, etc., kaolinite clay can also be used to synthesize zeolite molecular sieves and fillers for daily chemical products.
Is it better to choose a Raymond mill or a ball mill when grinding kaolin?
With the increasing demand for kaolin, the demand for kaolin grinding equipment has also risen steadily. Users who want to buy kaolin grinding equipment do not know how to choose. Should we choose a Raymond mill or a ball mill?
The following CLIRIK will briefly analyze the difference between Raymond mill and ball mill for everyone, hoping to help users when purchasing equipment.
The following CLIRIK will briefly analyze the difference between Raymond mill and ball mill for everyone, hoping to help users when purchasing equipment.
Raymond mills and ball mills are relatively common milling equipment, but the two types of equipment have different focuses, such as different looks, different capabilities, and different application fields. Users should choose according to their own needs. And conditions, to choose the equipment that suits you.
The advantage of the ball mill lies in its large processing capacity. The equipment is relatively simple to maintain and has a high degree of automation. You don't need to worry about it when working, just wait for the material to be processed. But the disadvantage is that it covers a large area, consumes a lot of electricity, and the granularity of the finished product is between 180-200 mesh.
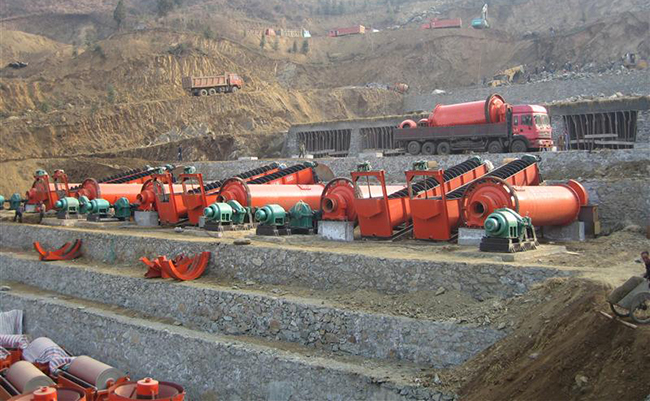
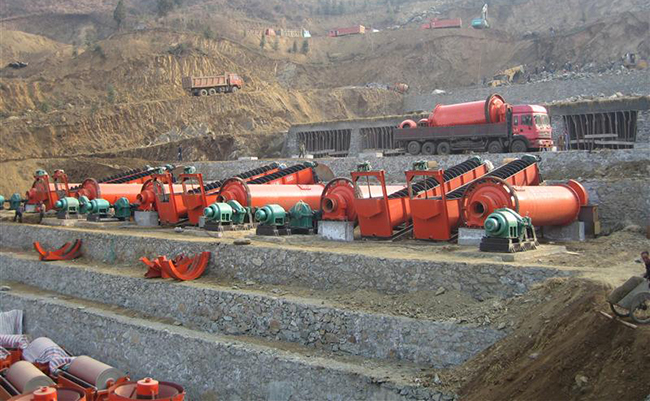
Ball Mill for Kaolin Powder
Compared with the ball mill, the Raymond pulverizer with a vertical structure has a greater advantage in terms of floor space, and the mesh number can be adjusted according to the needs of users, which is more energy-saving and energy-saving. Environmental protection, but the output is not as high as the ball mill, and the price is much lower.
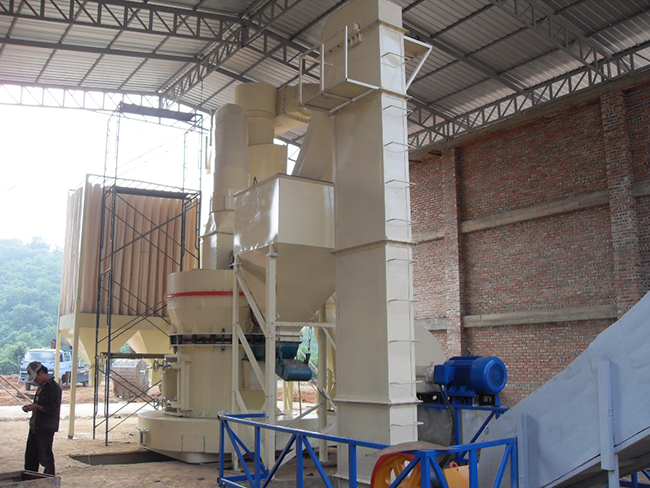
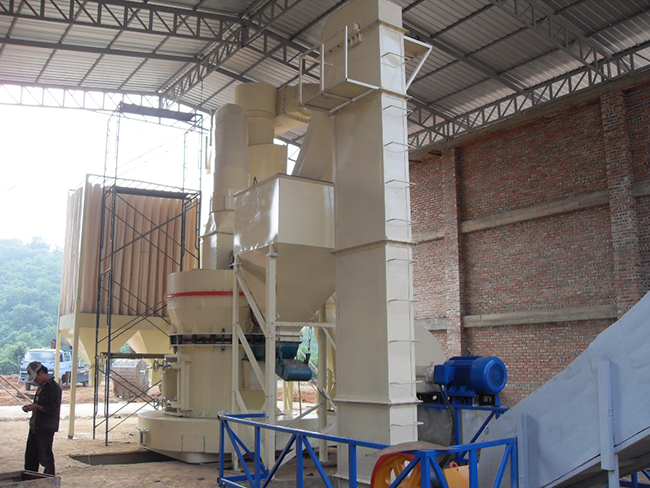
In principle, the ball mill uses the repeated rolling of the steel ball to complete the grinding, while the Raymond mill uses the cooperation of the roller mill and the grinding ring to grind the material. In terms of dust, Raymond mills are undoubtedly more environmentally friendly than ball mills. In terms of feeding, the Raymond mill has a certain advantage, because the Raymond mill can continuously feed and process materials, while the ball mill can only process materials batch by batch.
FAQ
Who we are?
Which models can be selected for processing ultra-fine powder?
How to get the latest quotation?
FAQ
Who we are?
Shanghai CLIRIK Machinery Co.,Ltd. has been committed to the field of ultra-fine powder grinding machines for 20 years.
CLIRIK has a first-class manufacturing base with standardized and intelligent production lines.
CLIRIK's professional R&D, sales, installation and after-sales teams have provided door-to-door services to more than 100 countries and regions.
Which models can be selected for processing ultra-fine powder?
HGM grinding mill: 74-5 micron(200-2500 mesh); D97=5 micron
YGM Raymond mill: 613-33 micron(30-325 mesh); D90=30 micron
CLUM vertical roller mill: 20-5 micron(600-3000 mesh); D50=2 micron D97=4 micron
How to get the latest quotation?
You can leave a message online or contact CLIRIK directly:
Email: sales@clirik.com
WhatsApp: +8613512155195/+8613917147829
Product List